Solving Common Issues in Brazing Joints
Brazing is an efficient and reliable method for joining metals, but occasional challenges can arise, affecting joint quality. This troubleshooting guide outlines practical solutions to common brazing issues, ensuring strong and durable connections.
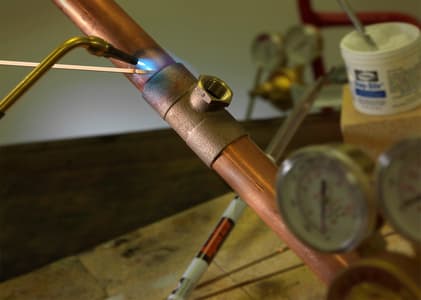
Brazing Joints
When the Brazing Alloy Doesn’t Flow into the Joint Despite Melting
- Insufficient Internal Heat:If the alloy forms a fillet but doesn’t penetrate the joint, it’s likely that only the outside is reaching brazing temperature. Always heat the tube first to transfer heat inside the fitting and achieve even temperature distribution.
- Flux Deterioration:Overheating can cause the flux to become saturated with oxides, preventing smooth alloy flow. Use a softer flame and apply a thicker layer of flux if needed. For prolonged heating or stainless steel applications, Harris Stay-Silv® black flux is recommended.
When the Brazing Alloy Forms Beads Instead of Spreading Across the Surface
- Improper Heating Technique:The base metals may not be reaching brazing temperature, while the torch flame melts the filler metal too soon. Ensure even heating to allow the filler metal to flow correctly.
- Surface Contamination:Dirt, oxidation, or grease on the base metals can prevent proper alloy adhesion. Always clean surfaces thoroughly before brazing.
When the Brazing Alloy Flows Away from the Joint Instead of Into It
- Incorrect Heat Application:Ensure the fitting reaches the appropriate temperature, and direct the torch flame toward it. This helps draw the filler metal into the joint rather than away from it.
When the Filler Metal Cracks After Solidifying
- Metal Expansion Differences:Dissimilar metals expand and contract at different rates, which can put stress on the filler metal as it cools. This issue often arises in copper-to-steel joints, where copper expands more than steel. A steel-into-copper assembly can help mitigate this issue.
- Brittle Phosphide Formation:Using a phosphorus-containing alloy on steel or ferrous metals can lead to brittle compounds, causing cracks. To avoid this, choose non-phosphorus brazing alloys for ferrous materials.
- Excessive Joint Clearance:A joint gap that is too wide can lead to cracking due to stress or vibration. Maintain a clearance of .002” - .006” at brazing temperature, depending on the alloy used.
- Rapid Cooling:Quenching the joint too quickly can cause cracks. Allow the joint to cool gradually before removing flux residue.
When the Joint Leaks During Operation
- Uneven Heating:If the joint isn’t heated uniformly, the filler metal won’t fully penetrate, leading to a weak or incomplete bond. Follow correct heating procedures to ensure proper joint formation.
- Overheating Issues:Excessive heat can cause essential elements like phosphorus and zinc to evaporate, weakening the joint.
- Incorrect Flame Adjustment:A poorly set torch flame may deposit carbon or cause excessive oxidation, negatively affecting the joint’s integrity.
By recognizing and addressing these common brazing challenges, you can enhance joint strength, improve process efficiency, and ensure reliable metal bonding.